Рд 34.30.605 Технологическая Инструкция По Замене Лопаток Паровых Турбин
Второе важное замечание. Описанные способы ремонта корпусов цилиндров и стопорных клапанов нужно рассматривать как технические рекомендации для принятия решения в ходе устранения конкретного выявленного дефекта. Более того, техническое решение о ремонте корпусов в каждом конкретном случае необходимо согласовывать с заводом-изготовителем и с головными институтами РАО 'ЕЭС Россия' — ВТИ и ЦНИИТМАШ. ВОПРОСЫ ДЛЯ САМОПРОВЕРКИ 1.
Какие узлы турбины наиболее целесообразно ремонтировать в заводских условиях? Перечислите основные характерные дефекты литых цилиндров и корпусов клапанов. Перечислите основные направления работ по продлению срока службы литых цилиндров и корпусов клапанов. Перечислите зоны максимально вероятного возникновения трещин в корпусах цилиндров и клапанов.
ЗАКЛЮЧЕНИЕ Анализ состояния систем организации ремонта паровых турбин в условиях ТЭС, а также в условиях заводов — изготовителей выявил ряд проблемных вопросов, которые, с точки зрения авторов, требуют дальнейшей углубленной проработки и совершенствования. К таким вопросам по мнению авторов относятся (укрупненно): — Разработка технических условий на ремонт и ремонтных формуляров всего парка турбин. — Совершенствование оснастки, применяемой для ремонта турбин.
Feb 1, 2011 - РД 08r492r02 Инструкция о порядке ликвидации, консервации скважин. Со 34.30.605 Инструкция по замене лопаток паровых турбин. (РД 34.30.605) Технологическая инструкция по замене лопаток паро. Тилиндры турбины паровой.
— Применение новых материалов, а на их основе уточненных технологий для восстановления деталей турбин, обеспечения плотности соединения сопрягаемых деталей и так далее. — Разработка технологий восстановительной термообработки литых деталей турбин, отработавших свой ресурс.
— Совершенствование алгоритмов расчета влияния теплового состояния трубопроводов и их опорно-подвесной системы на работу турбоустановки, так как на большинстве эксплуатируемых турбоагрегатов наблюдаются повышенные усилия от присоединенных трубопроводов, что приводит к нарушениям в работе турбин (повышенная вибрация, стесненность тепловых расширений). — Автоматизация задач сетевого планирования ремонтных работ. — Решение комплекса вопросов по поузловому заводскому ремонту оборудования. — Разработка, апробация и реализация комплексной системы мониторинга состояния турбоустановки, которая позволит обоснованно перейти к организации ремонта оборудования ТЭС, в частности паровой турбины, по состоянию 151, 152. При этом авторы считают мониторинг состояния более широким понятием, включающим в себя как одну из задач — диагностику.
Считаем, что вышеприведенный перечень может (и должен) сориентировать студентов (будущих инженеров), а также слушателей курсов переподготовки и повышения квалификации персонала ТЭС на активизацию разработок в указанных направлениях. ГЛОССАРИЙ Адгезия — слипание разнородных твердых или жидких тел (фаз), соприкасающихся своими поверхностями. Адгезия обусловлена межмолекулярным взаимодействием. Акт 'скрытых работ' — документ, составляемый на все конструкции и их элементы, закрываемые в процессе производства работ, к которым в дальнейшем не будет доступа. Борштанга — оправка для крепления сменных резцов при обработке (расточке) отверстий на токарных, сверлильных, расточных и других станках. При ремонте борштанга применяется для определения взаимного расположения деталей статора и ротора турбины.
Выработка посадочного места — любые механические повреждения посадочной поверхности в результате перемещения сопрягаемых деталей в процессе эксплуатации механизма. Дефектация — выявление всех дефектов и отклонений геометрических размеров и формы. Обработать 'как чисто' (пропылить поверхность) — исправление геометрии поверхности детали механической обработкой (токарная, фрезерная, шлифовальная) с минимальным съемом стружки с обрабатываемой поверхности. Кантовка (от немецкого kanten — переворачивать) — операция по изменению пространственного положения детали с помощью грузоподъемных механизмов. Контрольная плита — средство измерения плоскостности поверхности.
Колено (коленчатость) — несовпадение взаимно параллельных осей пары роторов. Маятник — излом осей (угловое несовпадение осей) пары собранных роторов с жесткой муфтой. Наброс нагрузки — резкое увеличение нагрузки турбоагрегата. 'Наделка' — установка дополнительной неподвижной прокладки (с помощью сварки, резьбового соединения и т. Д.) на деталь с целью изменения ее геометрических размеров. Натяг — разность между диаметром вала и отверстия, когда диаметр вала превышает диаметр отверстия (до сборки). Применяется для получения неподвижного соединения путем нагревания детали с отверстием перед посадкой на вал.
Натянутый металл (баббит) — пластические изменения формы поверхности металла в результате механических воздействий (ударов). Обтяжка 'на горячо' (крепежа) — создание натяга в резьбовом соединении с помощью удлинения шпильки (болта) нагреванием и подтяжкой гайки в горячем состоянии. Окалина — продукт окисления, образующийся на поверхности стали и некоторых других сплавов при нагреве на воздухе или в других средах, содержащих кислород. Окалина состоит из окислов металлов; она ухудшает качество поверхности и приводит к потерям металла. Удаляют окалину механическим и химическим путем. 'Подрез' — локальное уменьшение линейного размера детали в результате механических воздействий (проточки, ударов, газовой резки, воздействия рабочей среды и т. Пины — цилиндрические стержени, устанавливаемые в одну из деталей для фиксации ее положения относительно другой детали при сборке.
Проверка по краске — технологическая операция по определению прилегания одной поверхности к другой или правильности геометрической формы поверхности. При выполнении проверки на одну из поверхностей собираемых деталей или контрольный инструмент (контрольную плиту, калибр и т. Д.) наносится краска, и качество прилегания проверяется по отпечаткам краски на ответной поверхности. Призонные болты (отверстия) — цилиндрический или конический болт для неподвижного соединения деталей и фиксации их взаимного расположения при сборке. Пригонка зазоров — технологическая операция по доведению зазоров в уплотнениях до требований чертежа или ремонтного формуляра. Рым — металлическое кольцо, закрепляемое на машинах (и их частях) и предназначенное для захвата и перемещения их при монтаже, разборке или транспортировании. Разделка паза — финишная обработка поверхности шпоночного паза (или другого паза), предварительно обработанного резанием, снятием тонкой стружки шабером вручную или механическим путем.
Применяется для точного сопряжения шпоночного соединения. Растолкать ротор — переместить ротор, находящийся в собственных подшипниках, в осевом направлении с целью определения парового, масляного разбега ротора или создания зазора между муфтами для беспрепятственной выемки ротора из проточной части.
Сборка 'насухо' — контрольная сборка механизма без применения уплотняющих материалов. Свищ — сквозное повреждение трубопровода или сосуда. Сдача 'на чистоту' — стандартная операция по проведению скрытых работ; заключается в предъявлении заказчику (или другому ответственному лицу) внутренних полостей собираемого механизма (сосуда, трубопровода и т. Д.) на отсутствие посторонних предметов. Талреп — приспособление для натягивания снастей (морской), для настройки грузоподъемного приспособления.
Траверса — приспособление для подъема в нужном пространственном положении груза с несимметричным расположением центра тяжести. Формуляр (паспорт) — бланк для занесения сведений о результатах контроля состояния узлов оборудования перед ремонтом и после проведения ремонтных и пригоночных работ. Холостой ход — движение механизма или машины, при котором не совершается полезная работа. Шабровка (шабрение) — отделочная обработка поверхности, предварительно обработанной резанием, снятием тонкой стружки шабером вручную или механическим путем.
Применяется для точного сопряжения деталей, например для герметизации соединений. Шабрят плоские или цилиндрические поверхности деталей подвижных или неподвижных соединений, когда необходимо обеспечить точное сопряжение, точное относительное положение деталей или создать герметичное соединение. СПИСОК ЛИТЕРАТУРЫ.
Надежность теплоэнергетического оборудования ТЭС и АЭС / Под ред. М.: Высшая школа, 1991. Штромберг Ю.Ю., Терентьев И.А. Итоги работы энергоблоков ТЭС в период 1993—1997 годов // Электрические станции. Терентьев И.
Оценка надежности турбин энергоблоков мощностью 300, 800 и 1200 МВт // Электрические станции. Штромберг Ю.Ю., Понасечкин С.А., Копсов А.Я. Повреждаемость теплоэнергетических блоков мощностью 300 МВт // Электрические станции. Бродов Ю.М., Мурманский Б.Е., Мительман М.М.
Анализ показателей надежности турбоустановок и энергоблоков в целом АО 'Свердловэнерго' // Теплоэнергетика. Показатели надежности основного и вспомогательного оборудования турбоустановок ТЭС Свердловэнерго / Бродов Ю.М., Мурманский Б.Е., Мительман М.М. // Электрические станции.
Трухний А.Д. Стационарные паровые турбины. М.: Энергоиздат, 1990.
Паровые и газовые турбины / Трубилов М. А., Арсеньев Г. В., Фролов В. И др.; Под ред. Костюка и В.В. М.: Энергоиздат, 1985. Костюк А.Г.
Динамика и прочность турбомашин: Учебник для вузов. М.: Издательство МЭИ, 2000.480с. Бененсон Е.И., Иоффе Л.С. Теплофикационные паровые турбины.
М.: Энергоатомиздат,1986. Паровые турбины малой мощности КТЗ / Кирюхин В. И., Тараненко Н. М., Огурцова Е. М.:Энергоатомиздат, 1987.
Инденбаум В.С., Случаев М. Ревизия и ремонт паровых турбин коммунальных электростанций. М.: М-во коммунал. Сверчков А.Н. Ремонт и наладка паровых турбин.
М.; Л.: Госэнергоиздат, 1954. Северов Н.Н. Ремонт роторов паровых турбин.
М.; Л.: Госэнергоиздат, 1959. Молочек В.А.
Ремонт паровых турбин. М.: Энергия, 1968. Новиков Б.Б., Леонтьев Е. В., Дроздов В.
Ремонт корпусов паровых турбин. М.:Энергия, 1977. Дон Э.А., Осоловский В.П. Расцентровка подшипников турбоагрегатов. М.: Энергоиздат,1994. Гольдин А.С. Устранение вибраций турбоагрегатов на тепловых электростанциях М.: Энергия,1980.
Вибрация роторных машин. М.: Машиностроение, 1999.
Абалаков Б.В., Банник В.П., Резников Б.И. Монтаж и наладка турбоагрегатов и вспомогательного оборудования. М.; Л., Энергия, 1966. Правила организации технического обслуживания и ремонта оборудования зданий и сооружений электростанций и сетей РДПр34-38-030-92. Методические указания по совершенствованию системы технического обслуживания и ремонта энергоблоков и энергоустановок ТЭС на основе ремонтного цикла с назначенным межремонтным ресурсом М.
У.РД 34.20.601-96 РАО 'ЕЭС России' с 01.06.96. Методика оценки технического состояния паротурбинных установок до и после ремонта и в периодмежду ремонтами РД 34.20.581-96 СП ОРГРЭС 1998.
Правила технической эксплуатации электрических станций и сетей Российской Федерации / Министерство топлива и энергетики РФ, РАО 'ЕЭС России': РД 34.20.501.95. М.:СПО ОРГРЭС, 1996. ГОСТ 18322—78. Система технического обслуживания и ремонта техники. Термины и определения. Перминов И.А., Орлик В.Г., Гординский А.А.
Диагностика состояния проточных частей мощных паровых турбин с применением станционных вычислительных комплексов // Труды ЦКТИ. 27.Розенберг С.Ш., Хоменок Л.А., Эгерман В.Н. Диагностика состояния радиальных зазоров турбины К-800-240-3 в процессе эксплуатации. Методы диагностирования // Труды ЦКТИ. 28.Урьев Е.В., Мурманский Б.Е., Бродов Ю.М.
Концепция системы вибрационной диагностики паровой турбины // Теплоэнергетика. Опыт внедрения системы вибродиагностического контроля турбоагрегатов / Зиле А.3., Руденко М.Н., Томашевский С.Б. // Энергетик. Алгоритм подсистемы диагностики термонапряженного состояния корпусов ЦВД и ЦСД турбиныК-300-240-2 ХТЗ / Трухний А.Д., Грак В.Г., Берлянд В.И. // Тезисы докл. Опыт создания и освоения автоматизированных систем и подсистем диагностического контроля энергоблоков ТЭС / Лейзерович А.Ш., Сафонов Л.П., Гординский А.А. // Труды ЦКТИ.
Разработка и внедрение системы функционирования АСТД в составе АСУТП энергоблока 800 МВт Запорожской ГРЭС / Сафонов Л.П., Журавель А.М., Литвинов В.К. // Труды ЦКТИ.

33.Лейзерович А.Ш. Первый опыт создания экспертных систем для тепловых электростанций // Электрические станции. Expert system, flexible software maintain high performance levels at powerplant / Elliot Tom // Hjwer. 35.Андрюшин А.В. Совершенствование планирования и управления проведением ремонтных работ на энергетическом оборудовании // Вестник МЭИ. Методические указания по разработке и применению системы сетевого планирования и управления приремонте оборудования электростанций / Минэнерго СССР 30.06.76.
Пути совершенствования системы ремонта энергетических установок / Андрюшин А.В., Стенин В.А., Тимошенко Н.Н., Терещенко О.Г. // Вестник МЭИ.
РД 34.20.602-98 Основные положения и требования договора на выполнение работ по ремонту оборудования электростанций. ГОСТ 3.1109—82.
Термины и определения основных понятий. Физический энциклопедический словарь. М.: Советская энциклопедия, 1960.
Физический энциклопедический словарь. М.: Советская энциклопедия, 1963.
Физический энциклопедический словарь. М.: Советская энциклопедия, 1966. Неразрушающие испытания: Справочник: В 2 т / Под ред. М.; Л.: Энергия, 1965. ГОСТ 27.002—89.
Надежность в технике. Основные понятия. Термины и определения. Надежность и эффективность в технике: Справочник: В 10 т / Под ред. М.: Машиностроение, 1986. РД 34.20.801-93.
Инструкция по расследованию и учету технологических нарушений в работе электростанций, сетей и энергосистем / ОРГРЭС. М., 1993, 20. Указания по заполнению кодированной части акта расследования нарушения работоспособности теплоэнергетического оборудования / ОРГРЭС. РД 34.08.552-93. Методические указания по составлению отчета электростанции и акционерного общества энергетики и электрофикации о тепловой экономичности оборудования / ОРГРЭС. Методические указания по составлению отчета электростанции об использовании оборудования энергоблока / ОРГРЭС.
РД 34.20.801-2000. Инструкция по расследованию и учету технологических нарушений в работе энергосистем, электростанций, котельных, электрических и тепловых сетей. М.: Энергосервис 2001. 51.Жученко Л.А., Кортенко В.В., Данда В.И. Организация сбора и обработки информации по повреждаемости элементов проточной части // Совершенствование теплотехнического оборудования ТЭС, внедрение систем сервисного обслуживания, диагностирования и ремонта / Екатеринбург: УГТУ—УПИ, 2002.
Анализ работы энергетических блоков мощностью 150—1200 МВт за 1986—95 годы / СПО ОРГРЭС. Обзоры повреждений тепломеханического оборудования электростанций с поперечными связями итепловых сетей за 1986—95 годы / СПО ОРГРЭС. М.,.
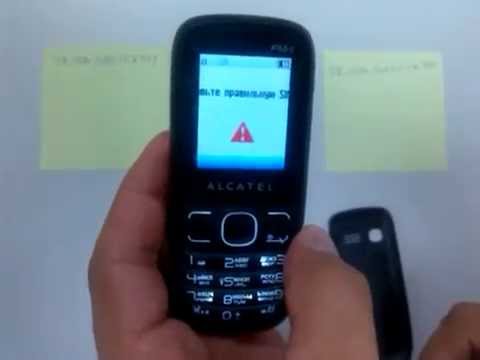
Анализ показателей надежности теплообменных аппаратов ТЭС / Бродов Ю.М., Резникова Р.С., Краснова Г.И., Чайка А.И. // Энергомашиностроение. 55.Жирицкий Г.С. Конструкция и расчет на прочность деталей паровых турбин. М.: Госэнергоиздат, 1960.311с.
Паровые турбины и конденсационные устройства. Теория, конструкции и эксплуатация. М.: Госэнергоиздат, 1954. 57.Трухний А.Д., Крупенников Б.Н., Петрунин С.В. Атлас конструкций паровых турбин. М.: МЭИ, 2000. Паровая турбина К-300-240 ХТГЗ / Под ред.
М.: Энергоатомиздат, 1982. Паровая турбина К-500-240 ХТГЗ / Под ред. М.: Энергоатомиздат, 1984. Паровые турбины сверхкритических параметров ЛМЗ / Под ред. Огурцова, В.К. М.:Энергоатомиздат, 1991.
61.Бауман Н.Я., Яковлев М.И., Свечков И.Н. Технология производства паровых и газовых турбин. М.: Машиностроение, 1973. Бодашков Н.К. Аварии паровых турбин и борьба с ними. М.: Госэнергоиздат, 1948.
Швецов П.Д. Предупреждение аварий паровых турбин М.: ГНТИ Машиностроительной литературы, 1953. РД 153.34.1.17.421-98 РД 10-262-98. Типовая инструкция по контролю и продлению срока службы металлаосновных элементов котлов, турбин и трубопроводов тепловых электростанций / ОРГРЭС. РД 34.17.440-96. Методические указания о порядке проведения работ при оценке индивидуального ресурса паровых турбин и продлении срока их эксплуатации сверх паркового ресурса. М.: ВТИ, 1996.
РД 34.17.436-92. Индивидуальный контроль металла литых корпусных деталей паровых турбин тепловых электростанций / МУ АООТ ВТИ. Инструкция по контролю поверхности литых корпусных деталей паровых турбин электростанций доначала эксплуатации: 108.2700-01-87 РД 34.17.402-87 Минэнерго 15.01.87 Минэнергомаш 26.01.87. Методические указания по проведению ультразвукового контроля крепежа энергооборудованияМУ 34-70-081-84 СПО Союзтехэнерго 1985 г.
РД 34.17.415-96. Инструкция по проведению ультразвукового контроля крепежа энергооборудования/СПО ОРГРЭС. Ремонт покоробленных корпусов паровых турбин РТМ 108.021.55—77 Минэнерго СССР. Исправление дефектов в литых корпусных деталях паровых турбин и арматуры методом заварки безтермической обработки. РД 108.021.112-88 МУ НПО ЦКТИ с 01.07.88. Инструкция по технологии ремонтной заварки корпусных деталей паровых турбин и арматуры перлитными электродами без термической обработки. И 34-70-020-85 РД 34.17.206-85 с изм.
1 Главтехуправление Минэнерго СССР, 12.02.85. РД 153.34.1-17-458-98. Методика определения возможности эксплуатации с трещинами и выборкамилитых корпусов деталей турбин с давлением пара более 9 МПа / АООТ ВТИ 1999. Быстрицкий Н.
Диафрагмы паровых турбин. М.: Машгиз, 1958. 5895205 США, МПК F 01 D 1/2. Технология ремонта турбинных диафрагм.
Анализ повреждаемости роторов, подшипников и систем маслоснабжения паровых турбин / Мурманский Б.Е., Плотников П.Н., Руденко А.С., Демшин В.И. // Совершенствование турбин и турбинного оборудования: Регион, сб. Екатеринбург, 2000. РД 34-30-506-90. Методические указания по нормализации тепловых расширений паровых турбин тепловых электростанций / Гл. Научно-техническое управление Минэнерго. РД 34.17.406-82.
Инструкция по контролю роторов паровых турбин со стороны осевого канала / Главтехуправление Минэнерго. О предупреждении повреждений роторов высокого и среднего давления турбин ТЭС (центральных полостей роторов) Ц-05-97 (т) // РАО 'ЕЭС России'. РД 34.30.507-92. Методические указания по предотвращению коррозионных повреждений дисков и лопаточного аппарата паровых турбин в зоне фазового перехода / Управление научно-технического развития корпорации Росэнерго 03.04.92.
М., ВТИ, 1993. РД 34.17.450-98. Методические указания по ультразвуковому контролю без разлопачивания обода диска в районе верхних концентраторов Т-образного паза.
М.: ВТИ, 1999. РД 153-34.1-17.457-99. Методические указания по проведению акустико-эмиссионного контроля цель-нокованных роторов паровых турбин ТЭС. МУ 34-70-167-87. Методические указания по магнитопорошковой дефектоскопии коррозионно-по-врежденных рабочих лопаток паровых турбин в зоне фазового перехода. М.: ВТИ, 1987.
Инструкция по ультразвуковому контролю эррозийно-изношенных выходных кромок рабочих лопатоктурбин СПО Союзтехэнерго, 1979. РД 34.17.449-97. Методика вихретокового контроля лопаток паровых турбин тепловых электростанций дефектоскопом 'Зонд ВД-96'.
М., ВТИ, 1997. Левин А.В., Боришанский К.
Н., Консон Е. Прочность и вибрация лопаток и дисковпаровых турбин. М.: Машиностроение, 1981. О повреждениях рабочих лопатокпоследних ступеней роторов низкого давления. Амелюшкин В. Эрозия лопаток паровых турбин: прогноз и предупреждение: Учебное пособие.СПб.: Энерготех, 2000.

О восстановлении ресурса рабочих лопаток и дисков паровых турбин / Жученко Л.А., Кортенко В.В., Сахнин Ю.А., Ермолаев В.В. // Электрические станции. РД 153-34.1.17.424. Методические указания по расследованию причин повреждений деталей роторов паровой турбины. М., ВТИ, 2001. РД 34.30.605.
Технологическая инструкция по замене лопаток паровых турбин. М.: Союзтехэнерго,1985. РД 153-34.1-17.462-00. Методические указания о порядке оценки работоспособности рабочих лопатокпаровых турбин в процессе изготовления, эксплуатации и ремонта. М.: ВТИ: 2001.
Технология подварки шипов лопаток ИП 510-107 ЛМЗ. МУ 34-70-088-84.
Методические указания по определению расцентровок валопроводов турбоагрегатов: Изменение № 1 к вышеуказанному документу РД 34.30.601-84 Главтехуправление Минэнерго СССР, 10.08.89Главтехуправление Минэнерго СССР, 24.10.91. Шостакович Б.В. Методика центровки паровых турбин. М.: Госэнергоиздат, 1950. О сборке, центровке муфт и системы РВД-РСД турбин К-300-240 ХТЗ и К 200-130 ЛМЗ эксплуатационный циркуляр Ц-05-84 (т) Главтехуправление по эксплуатации энергосистем, апрель 1984 г. Центровка подшипников турбоагрегата без разборки муфтовых соединений валопровода / Дон Э.А.,Конторович Т.С., Олимпиев В.И., Мейерович Г.М. // Теплоэнергетика.
Сушко Е.А., Авруцкий Г.Д. Центровка валопровода турбоагрегатов взвешиванием без разборки муфт//Энергетик. Бодашков Н.К.
Эксплуатация паровых турбин. М.; Л.: Государственное энергетическое издательство, 1955. Шаргородский В.С., Хоменок Л.А., Курмакаев М.К.
Нормализация тепловых расширений мощных паровых турбин // Электрические станции. Нормализация тепловых расширений паровых турбин / Авруцкий Г.Д., Дон Э.А., Людомирский Б.Н.,Савенкова И.А., Березин М.Г.
// Совершенствование теплотехнического оборудования ТЭС, внедрение систем сервисного обслуживания, диагностирования и ремонта. Екатеринбург: УГТУ-УПИ, 1999. Сборник распорядительных документов по эксплуатации энергосистем. Курмакаев М.К. Мероприятия, обеспечивающие свободу тепловых расширений цилиндров мощных паровых турбин // Совершенствование теплотехнического оборудования ТЭС, внедрение систем сервисного обслуживания, диагностирования и ремонта.
Екатеринбург: УГТУ-УПИ, 1999. О скольжении корпусов подшипников паровых турбин / Авруцкий Г.Д., Браун Э.Д., Дон Э.А. Опыт освоения головных турбоустановок энергоблоков мощностью 800 МВт / Моногаров Ю.И., Орлов И.И., Розенберг С.Ш. // Энергомашиностроение. Исследование силового взаимодействия корпусов цилиндров и подшипников турбин К-800-240-3 / Розенберг С.Ш., Хоменок Л.А., Кметь А.И.
// Теплоэнергетика. Водичев В.И., Губанов Д.Е., Сурис П.Л.
О работе поперечных шпоночных соединений цилиндров и корпусов подшипников паровых турбин // Теплоэнергетика. Улучшение эксплуатационных характеристик турбин Т-250/300-240 на ТЭЦ-22 / Шаргородский В. С.,Ковалев И.А., Розенберг С.Ш., Хоменок Л.А., Козлов И.С., Кочуров С.Н., Зуев О.Г. // Электрические станции.
Розенберг С.Ш., Хоменок Л.А., Ильин В.И. О силовом взаимодействии цилиндров икорпусов подшипников турбины К-300-240 ЛМЗ // Электрические станции.
Розенберг С.Ш., Сафонов Л.П., Хоменок Л.А. Исследование мощных паровых турбин на электростанциях.
М.: Энергоатомиздат, 1994. Обеспечение температурных расширений цилиндров турбин при реконструкции энергоблоков / Дон Э. А., Авруцкий Г.Д., Потапов Е.Н., Бурлака Л.В., Лучников В.А., Сорока В.Ф. // Энергетик. Жорник В.И., Калиниченко А.С., Кезик В.Я., Кобзарь Ю.В., Кот А.А.
Рекомендации по ремонту и реконструкции тяжелонагруженных узлов скольжения с использованием композиционных материалов. Минск: Институт технической кибернетики НАН Беларуси, 2000. 113.Авруцкий Г.Д., Дубровский С.Л., Савенкова И.А.
Металлофторопластовая лента на поверхностях скольжения корпусов подшипников турбин // Теплоэнергетика. Совершенствование (восстановление) показателей температурных расширений цилиндров паровыхтурбин при пуско-остановочных режимах / Дон Э.А., Авруцкий Г.Д., Михайлова А.Н., Савенкова И.А., Буг-лаев К.Е. // Электрические станции. ТУ РБ 100649721.030-2000. Элементы пар скольжения из литого композиционного материала.
Применение твёрдосмазочных покрытий для нормализации температурных расширений цилиндров паровых турбин /Дон Э.А., Михайлова А.Н., Складчиков В.П., Назимов Е.И. // Энергетик.
Опора корпуса турбомашины / Л.А. Хоменок, В.С. Шаргородский, С.Ш.
Ремезов А.Н., Куличихин В.В., Хоменок Л.А. Исследование силового взаимодействия элементов турбины К-1200-240-3 на Костромской ГРЭС//Энергосбережение и водоподготовка. Устройство для обеспечения теплового расширения турбоагрегата / Я.И. Курмакаев М.К., Новиков В.М., Рабинович Э.М. Новая подвеска клапанов ЦСД турбины К-300-240 ЛМЗ // Теплоэнергетика. 1321846 СССР.
Опора цилиндра турбины / В.А. Персидский Б.И.
№ 25.122.Липсман С.И., Музыка А.Т., Липсман В.С. Предупреждение и устранение вибрации роторных машин. Киев: Техника, 1967. Исследование и устранение вибрации паровых турбоагрегатов. М.: Энергоиздат, 1982.
Кальменс В.Я. Обеспечение вибронадежности роторных машин на основе методов подобия и моделирования.
СПб.: СЗПИ, 1992. Основы надежности и технической диагностики турбомашин: Учеб.
Пособие / Екатеринбург: УГТУ, 1996. РД 24.033.04-88.
Методика комплексных вибрационных испытаний энергетических паротурбинных агрегатов / Минэнерготяжмаш. ГОСТ 23364—88.
Агрегаты паротурбинные стационарные. Нормы вибрации и общие технические кпроведению измерений / Госстандарт. 128.Олимпиев В.И.
Влияние погрешностей изготовления и монтажа на спектр вибрации турбоагрегата // Труды ЦКТИ, 1980. Myтуль В.В., Орлик В.Г.
Влияние люфтов в сочленениях подвески на вибрационную надежность регулирующих клапанов паровых турбин // Труды ЦКТИ, 1980. Коваль Г.С., Кузнецов Б.Д.
Контроль величины колебаний роторов при пуске турбоагрегатов // Повышение надежности и экономичности энергоблоков. Челябинск, 1973.Вып. Причины повышенного уровня составляющих второй гармоники в спектре колебаний опор мощных турбогенераторов // Вибрационная надежность паротурбинных агрегатов. Салимон А.В., Рузский В.А., Полищук Г.А. Диагностика места изменения распределенного дисбаланса валопровода турбоагрегата и задеваний ротора о статор // Вибрационная надежность паротурбинных агрегатов: Сбор.
Коваль Г.С., Урьев А.В., Львов М.И., Манькович Я.Д. Влияние дефектов соединения роторов на их вибрационное состояние / Вибрационная надежность паротурбинных агрегатов: Сб. Израилев Ю.Л., Зиле А.3., Микунис О.С., Лубны-Герцык А.Л., Тривуш В.И.// Вибрационный контроль за развитием трещин в роторах паровых турбин / Вибрационная надежность паротурбинных агрегатов: Сб. Дон Э.А., Авруцкий Г.А. Выявление повреждений муфтового соединения трехопорной системы РВД-РСД паровых турбин средствами вибрационной диагностики // Вибрационная надежность паротурбинных агрегатов: Сб.
Банник В.П., Случаев М.А. Монтаж паровых турбин. М.: Госэнергоиздат, 1959. Винокуров И.В.
Опыт диагностики состояния турбоагрегата по спектру вибрации // ТрудыЦКТИ. Олимпиев В.И., Голод И.Л. Влияние подшипников скольжения на полигармоническую вибрацию энергетического турбоагрегата//Труды ЦКТИ. 139.Олимпиев В.И. Фоновый спектр вибрации и вибродиагностика неисправностей энергетического турбоагрегата // Труды ЦКТИ. Олимпиев В.И., Голод И.Л. Анализ спектра вибрации математической модели ротора с трещиной на подшипниках скольжения // Труды ЦКТИ.
Винокуров И.В., Медведь В.С. Диагностические признаки в вибрационном поведении действующих паротурбинных агрегатов // Труды ЦКТИ. Тимошенко С.П.
Колебания в инженерном деле. М.: Госиздатфизматлитературы, 1959. МУ 34-70-162-87. Методические указания по балансировке многоопорных валопроводов турбоагрегатов на электростанциях / Союзтехэнерго, 1988.
Методические указания по динамической балансировке роторов на станке маятникового типа РД34.30.602 ОРГРЭС 1975. Агапов А.П., Балашов А.М., Фрегейт Р.А. Ремонт, наладка и испытания систем регулирования паровых турбин. М.: Энергия, 1976. Энгель-Крон И.В. Ремонт паровых турбин. М.: Энергоиздат, 1981.
Карасю к В.А., Балашов А.М. Ремонт и наладка систем регулирования теплофикационныхтурбин.
М.: Энергоиздат, 1994.
Утверждено Департаментом научно-технической политики и развития РАО ЕЭС России 30 сентября 2001 года МЕТОДИЧЕСКИЕ УКАЗАНИЯ ПО РАССЛЕДОВАНИЮ ПРИЧИН ПОВРЕЖДЕНИЙ ДЕТАЛЕЙ РОТОРОВ ПАРОВЫХ ТУРБИН ЭЛЕКТРОСТАНЦИЙ РД 153-34.1-17.424-2001 Взамен РД 34.17.424-87 Срок действия установлен с 1 января 2002 года до 1 января 2012 года Разработано Департаментом научно-технической политики и развития РАО ЕЭС России; Всероссийским теплотехническим научно-исследовательским институтом (ОАО ВТИ). Исполнители: В.В.
Панферов (РАО ЕЭС России), В.Ф. Резинских, В.А. Комаров, А.М. Клыпина (ОАО ВТИ), Л.А.
Жученко (ОАО ТМЗ), О.Н. Симин (ОАО ЛМЗ), Ф.М. Сухарев (ОАО Турбоатом), В.Н. Чеботарев (АО КТЗ), Ю.Е. Миненков (ОАО Тюменьэнерго), Ю.А. Букин (ОАО Тюменьэнергоремонт), П.Р. Должанский (ЦРМЗ АО Мосэнерго), В.В.
Глухов (Представительство Центрэнерго), В.Н. Судаков (ОАО Фирма ОРГРЭС). Утверждено Департаментом научно-технической политики и развития РАО ЕЭС России.
Первый заместитель начальника А.П. Срок первой проверки РД - 2007 г. Периодичность проверки - один раз в 5 лет.
Настоящий руководящий документ по расследованию причин повреждений деталей роторов паровых турбин электростанций распространяется на паровые турбины и устанавливает основные требования организации и проведения контроля за состоянием металла деталей после их повреждения в процессе эксплуатации. Положения настоящего руководящего документа подлежат обязательному применению на предприятиях отрасли Электроэнергетика, расположенных на территории Российской Федерации, и могут быть использованы предприятиями и объединениями предприятий, в составе (структуре) которых независимо от форм собственности и подчинения находятся тепловые станции. Руководящий документ может быть распространен на паровые турбины, установленные на предприятиях других отраслей. ОБЩИЕ ПОЛОЖЕНИЯ 1.1. Настоящий документ устанавливает порядок и основные требования к организации расследования причин повреждения деталей проточной части паровых турбин электростанций (эксплуатирующихся в соответствии с нормативами предприятий-изготовителей), которые должны быть учтены при разработке мероприятий по устранению и предотвращению аналогичных повреждений, а также при определении возможности дальнейшей эксплуатации турбин. При этом следует руководствоваться имеющимися нормативными документами, указанными в Приложении Б.
Общие требования к организации и оформлению актов расследования, классификации аварий и отказов в работе установлены Инструкцией по расследованию и учету технологических нарушений в работе энергосистем электростанций, котельных, электрических и тепловых сетей (приложение А РД 153.34.0-20.801). В состав комиссии по расследованию причин повреждений, назначенной в установленном порядке, должны быть включены специалисты по эксплуатации турбоустановки, металловедению, расчетам на прочность и представители предприятия-изготовителя. В зависимости от характера повреждения (разрушения) в нее могут войти специалисты по вибрации, водно-химическому режиму, коррозии, эрозии, устройствам тепловой защиты, автоматике. Причины повреждения металла деталей анализируются и устанавливаются по результатам обследования. В тех случаях, когда для принятия окончательного решения требуется проведение более глубоких лабораторных исследований, составляется единая программа с участием необходимых специалистов. При этом комиссия обязана подготовить предварительное заключение и установить срок выдачи окончательного заключения о причинах повреждения. Комиссия должна получить от предприятия-изготовителя необходимую техническую документацию: технические условия на поставку поврежденной детали (деталей), паспортные данные, чертежи, расчеты на прочность.
Администрация электростанции до начала работы комиссии должна принять меры по сохранению обстановки в месте повреждения, провести опрос персонала, подготовить доклад для комиссии о произошедшем нарушении работы турбины в соответствии с Инструкцией, указанной в п. Обозначение НД Наименование НД Номер пункта ГОСТ 1497-85 Металлы. Методы испытания на растяжение Приложение Ж ГОСТ 5632-72 Стали высоколегированные и сплавы коррозионно-стойкие, жаростойкие и жаропрочные. Марки и технические требования Приложение В ГОСТ 9454-78 Металлы. Метод испытания на ударный изгиб при пониженных, комнатной и повышенных температурах Приложение Ж ОСТ 108.020.03-82 Заготовки лопаток турбин и компрессоров штампованные из коррозионно-стойкой и жаропрочной стали. Приложение Б (рекомендуемое) ПЕРЕЧЕНЬ ОСНОВНЫХ НОРМАТИВНЫХ ДОКУМЕНТОВ, ИСПОЛЬЗУЕМЫХ ПРИ КОНТРОЛЕ ЗА МЕТАЛЛОМ ПОВРЕЖДЕННЫХ ДЕТАЛЕЙ ПАРОВЫХ ТУРБИН 1.
ГОСТ 18442-80. Контроль неразрушающий. Капиллярные методы.
Общие требования. ГОСТ 21105-87. Контроль неразрушающий. Магнитно-порошковый метод. ОСТ 21105-87. Контроль неразрушающий. Методы акустические.
Общие положения. РД 17.409-82. Инструкция по ультразвуковому контролю лопаток паровых турбин. ГОСТ 12503-75. Методы ультразвукового контроля. Общие требования.
Методические рекомендации. Оборудование энергетическое. Расчеты и испытания на прочность. Расчет коэффициентов интенсивности напряжений. Рекомендации по контролю микроструктуры металла методом оттисков. (М.: СЦНТИ ОРГРЭС, 1969).
ОСТ 34-70-690-96. Метал паросилового оборудования электростанций.
Методы металлографического анализа в условиях эксплуатации. Временная инструкция по выявлению трещиноподобных дефектов в тепловых канавках роторов турбин индикаторами ИГТ-02 (М.: ВТИ, 1989). РД 34.17.421-92. Контроль галтелей дисков цельнокованых роторов.
Инструкция и методика по контролю осевых каналов роторов турбин вихретоковым комплексом Ротор - Свердловск (г. Челябинск: Урал ВТИ, 1991). РД 34.17.411-84. Методические указания по определению длительной прочности теплоустойчивых сталей методом горячей длительной твердости. ОСТ 108.004.109-96.
Металл паросилового оборудования электростанций. Методы металлографического анализа в условиях эксплуатации. РД 24.033.02-88. Методические указания. Лопатки стационарных паровых турбин. Расчет на прочность. РД 34.17.449-97.
Методика вихретокового контроля лопаток паровых турбин тепловых электрических станций дефектоскопом Зонд ВД-96. Информационное письмо ОАО ЛМЗ N 510-753-190. Указание по осмотру, контролю и ремонту роторов, рабочих колес, дисков, рабочих лопаток и корпусов низкого давления паровых турбин ОАО ЛМЗ.
Информационное письмо ОАО ТМЗ N ТМТ-116035. Инструкция по обследованию эрозионного износа рабочих лопаток 23(26), 24(27), 25(28) ступеней турбин Т-175/210-130, Т-185/220-130-2, ПТ-135/165-130, ПТ-140/165-130-2. Информационное письмо ОАО ТМЗ N ТМТ-115985. Инструкция по обследованию эрозионного износа рабочих лопаток последних ступеней турбин ПТ-50/60-130/7 (24 ст.), Т-50/60-130 (25 ст.), Т-60/65-130 (25 ст.), Т-100/120-130 (25, 27 ст.), Т-100/120-130-2 (25, 27 ст.), Т-100/120-130-3 (25, 27 ст.), Т-110/120-130-4 (25, 27 ст.), Т-110/120-130-5 (25, 27 ст.), Т-116/125-130-7 (25, 27 ст.), Т-118/125-130-8 (25, 27 ст.), Т-115/125-330-1 ( 25 ст.), ПТ-90/120-130/10-1 (25 ст.). Информационное сообщение N 156 ОАО ТМЗ N ТМТ-116326, 2000 г.
Инструкция по обследованию эрозионного износа рабочих лопаток 29(38), 30(39), 31(40) ступеней турбины Т-250/300-240. Информационное письмо ОАО ТМЗ N 2503.00159. Контроль травлением выходных кромок лопаток последних ступеней низкого давления паровых турбин. Инструкция АО КТЗ N 09574-10. Инструкция по проведению вибрационных испытаний облопачивания.
Проверка состояния лопаточного аппарата паровых турбин, п. Предотвращение повреждений рабочих лопаток последних ступеней паровых турбин из-за эрозии их выходных кромок. Инструкция по контролю за металлом котлов, турбин и трубопроводов. Министерство энергетики и электрификации СССР, Главтехуправление по эксплуатации энергосистем (М.: Союзтехэнерго, 1984). Циркуляр МВК Ц-07-83 (Т). Нормы качества свежего пара перед турбинами ТЭС на давление 12,8 и 23,5 МПа. РД 50-345-82.
Расчеты и испытания на прочность. Методы механических испытаний металлов. Определение характеристик трещиностойкости (вязкости разрушения) при циклическом нагружении. ГОСТ 25.506-85. Методы механических испытаний металлов. Определение характеристик трещиностойкости (вязкости разрушения) при статическом нагружении.
Методические указания. Расчеты и испытания на прочность. Порядок разработки межотраслевых методических указаний на методы расчета и испытаний. Приложение В (справочное) ОБОБЩЕННАЯ ХАРАКТЕРИСТИКА ПОВРЕЖДАЕМОСТИ ДЕТАЛЕЙ, ПРИМЕРНЫЙ ПЕРЕЧЕНЬ ПОВРЕЖДЕНИЙ И МЕРОПРИЯТИЯ ПО ПОВЫШЕНИЮ ИХ НАДЕЖНОСТИ В.1. Обобщенная характеристика повреждаемости деталей В.1.1. Статистика повреждений лопаточного аппарата турбоагрегатов России и СНГ показывает, что характер повреждаемости широк и разнообразен (таблицы В.1, В.2; рисунки В.1 - В.5). За 30 лет эксплуатации имели место повреждения лопаточного аппарата, приведшие как к серьезным разрушениям турбоагрегатов, машинных залов и пожарам (см.
Таблицу В.2), так и к авариям с меньшими последствиями, однако существенно влияющими на эксплуатацию турбинного оборудования (см. Таблицу В.1, рисунки В.3 - В.5).
Таблица В.1 Статистические данные о разрушениях рабочих лопаток последних ступеней РНД с обрывом или трещиной у корня ГРЭС Тип турбины Количество разрушений Конаковская К-300-240 6 Сырдарьинская К-300-240 7 Экибастузская К-500-240 5 Каширская К-300-240 2 Запорожская К-800-240 1 Среднеуральская К-300-240 1 Черепетская К-300-240 1 Углегорская К-800-240 1 Лукомльская К-300-240 2 Рязанская К-300-240 1 Азербайджанская К-300-240 1. Таблица В.2 Статистические данные о наиболее крупных авариях из-за вылета рабочих лопаток последних ступеней РНД, вызвавших разрушение турбоагрегата Год ГРЭС Станционный номер турбины Наработка до повреждений, тыс.
Ч 1972 Конаковская 1 1967 Среднеуральская 10 Конаковская 4 Черепетская 6 Сырдарьинская 4 То же 7 - 6 (После капитального ремонта) 1990 - 7 Экибастузская 5 Азербайджанская 1 8 (После капитального ремонта в 1987 г.) Примечание. На всех станциях установлены турбины К-300-240, кроме Экибастузской, на ней смонтирована турбина К-500-240. Изменение характера повреждаемости лопаточного аппарата турбоагрегатов ТЭС Рисунок В.2. Электростанции России и СНГ, на которых происходили повреждения лопаточного аппарата турбоагрегатов 800 МВт Рисунок В.3. Разрушение обода диска из-за задеваний 49-й ступени РНД-2 турбоагрегата К-800-240-3 (ст. N 6) Рязанской ГРЭС Рисунок В.4. Поврежденная 50-я ступень ЦНД-2 турбоагрегата К-800-240-3 (ст.
N 6) Рязанской ГРЭС Рисунок В.5. Эскиз и схема повреждений диска 18-й ступени РСД турбоагрегата Т-175/210-130 (ст. N 2) Барнаульской ТЭЦ-3 (02.03.96) Пожары и разрушения турбоагрегатов и машинных залов происходили при вылете группы рабочих лопаток последних ступеней ЦНД турбоустановок 300 и 500 МВт (см. Таблицу В.2). Коррозионные повреждения, пониженная частота в сети, эрозионный износ, наработка, приведшая к накоплению усталостных повреждений, дефекты и повреждения бандажных связей, качество свежего пара, ошибки и недостатки при эксплуатации - таков круг причин вышеуказанных масштабных аварий на Сырдарьинской, Азербайджанской и Экибастузской ГРЭС. Эти аварии породили научно-технические проблемы, связанные с необходимостью ограничить их разрушительные последствия для машинных залов электростанций и предотвратить поломки лопаток последних ступеней ЦНД под корень и др. Предлагаемые ВТИ противопожарные мероприятия ограничивают масштабы разрушений и отключают маслонасос по комплексному сигналу, имеющему высокие уровни виброскоростей по показаниям штатной аппаратуры.
Предложены пути уменьшения накопления повреждаемости металла при пусконаладочных работах, прорабатываются вопросы профилактики таких повреждений во время ремонтов. Весома роль повреждений лопаточного аппарата турбоагрегатов большой мощности. Повреждения цельнофрезерованного бандажа последней ступени ЦНД-1 турбоагрегата 1200 МВт Костромской ГРЭС (рисунок В.6) позволяют оценить уровень эрозионного износа вершин рабочих лопаток, при котором в реальных условиях с учетом периода освоения блока, временного характера активной нагрузки и конструктивных особенностей бандажа произошел отрыв металла вершины лопатки. Анализ таких повреждений важен также для быстроходных турбоагрегатов 1000 МВт, используемых в атомной энергетике, из-за унификации цилиндра низкого давления. Повреждения диска 4-й ступени РНД турбоагрегата 800 МВт Рязанской ГРЭС по заклепочному соединению (см. Рисунки В.3, В.4) заставляют их анализировать и разрабатывать средства контроля для конкретного типа повреждений.
Повреждение лопаток 2-й ступени РВД турбоагрегата 800 МВт Сургутской ГРЭС-2 с учетом особенностей вибросостояния турбоагрегата и наладки автоматов безопасности требует дальнейшей проработки вопроса о контроле качества облопачивания во время ремонта в условиях электростанции. Поиски оптимальных решений для снижения эрозионного износа вершин рабочих лопаток последних ступеней ЦНД турбоагрегатов 300 МВт ОАО Турбоатом с помощью парового щита (рисунок В.7), несмотря на существующий опыт, были неудачными и в результате были повреждены ступени турбоагрегатов не только Ставропольской ГРЭС (рисунок В.8). При дальнейшей эксплуатации необходимо учитывать повреждения рабочих лопаток ЦНД турбоагрегата 500 МВт Назаровской ГРЭС, произошедшие при наработке примерно 44 тыс. Ч при эксплуатации агрегата перед повреждением с пониженной частотой сети в энергосистеме. Эрозионный износ и силовой отрыв вершин рабочих лопаток и бандажа РНД-1 турбоагрегата К-1200-240-3 (ст.
N 9) Костромской ГРЭС Рисунок В.7. Схема установки парового щита на турбоагрегате К-300-240. Эрозионный износ вершин рабочих лопаток 3-го потока 5-й ступени ЦНД турбоагрегата К-300-240 (ст. N 1) Ставропольской ГРЭС Опыт эксплуатации турбин Т-175-130 и Т-185-130 до 60 тыс. Ч показал, что из 17 турбин этого типа имело место коррозионное растрескивание семи дисков 16-й и восьми дисков 18-й ступени в районе защелок. Три диска 18-й ступени имели повреждения в виде трещин коррозионного растрескивания под напряжением от верхних углов Т-образного паза обода. На двух турбинах разрушения ободов привели к тяжелым авариям.
Для предотвращения таких повреждений разработан и утвержден РД 34.17.450-98 Методические указания по ультразвуковому контролю (без разлопачивания обода диска) в районе верхних концентраторов Т-образного паза. Повреждения дисков и рабочих лопаток теплофикационных турбоагрегатов 175 МВт Омской ТЭЦ-5 и Барнаульской ТЭЦ-9 (см. Рисунок В.5), работающих в зоне фазового перехода, происходили при наличии галтельных концентраторов. Однако проблема соблюдения норм качества свежего пара продолжает влиять на процесс зарождения и развития таких повреждений. На повестке дня стоит вопрос о повышении качества свежего пара как средства, способствующего сокращению количества возможных повреждений рабочих лопаток и дисков, и доведении эксплуатационных нормативов, в том числе по показателю удельной электропроводности, до современных международных норм. На Сургутской ГРЭС-2 произошли две аварии рабочих лопаток последней ступени РНД-3 турбины К-800-240-5 (ст.
Причиной первой аварии явился обрыв рабочей лопатки 60-й ступени РНД-3 по отверстию второго ряда демпферной проволоки. Трещина развивалась от кромки отверстия в сторону входной кромки лопатки. Дефектоскопический контроль выявил еще на семи лопатках этой ступени трещины, идущие от кромок отверстий второго ряда демпферной проволоки, и на одной лопатке 55-й ступени - на расстоянии 40 мм от отверстия - трещину от входной кромки между стеллитовыми пластинами. Причиной второй аварии явился обрыв рабочей лопатки 35-й ступени РНД-1 на расстоянии 215 мм от бандажной полки. Дефектоскопическим контролем выявлены трещины длиной от 5 до 30 мм еще на семи лопатках этой ступени.
Все трещины развивались от входной кромки между верхним ярусом демпферной связи и бандажными полками, а зарождались между стыками стеллитовых пластин. Материал лопаток - мартенситная сталь 13Х11Н2В2МФ-Ш (ЭИ961-Ш), термообработанная на КП 75.
Профиль лопатки - 1400 мм, длина - 960 мм. Лопатки после первой аварии отработали 45 тыс. Ч, а после второй - 15 тыс. Исследования показали, что образование и развитие трещин в обоих случаях связано с наличием в лопатках подкаленных зон металла в районе припайки стеллитовых пластин. Структура этих зон - мартенсит твердостью 385 - 420 HB вместо структуры отпущенного сорбита твердостью 248 - 302 HB по ОСТ 108.020. Таким образом, образование трещин в лопатках связано с нарушениями технологии их изготовления, проявившимися в локальной подкалке металла в зоне стеллитовых противоэрозионных пластин на входной кромке. На рисунке В.9 показаны микроструктура металла с зонами повышенной травимости и трещины в стеллите лопаток 60-й ступени турбины К-800-240 Сургутской ГРЭС-2.
Макроструктура металла и трещина в стеллите рабочей лопатки 60-й ступени турбоагрегата К-800-240 Сургутской ГРЭС-2 В 70-х годах имели место такие же характерные повреждения лопаток из стали 15Х11МФ последних ступеней ЧНД турбин К-300-240 ОАО ЛМЗ. Пластины припаивались на предприятии-изготовителе ручным способом. После еще нескольких повреждений лопаток предприятиями-изготовителями было рекомендовано использовать автоматизированный процесс напайки стеллитовых пластин. В последующие периоды эксплуатации таких турбин разрушения лопаток по этой причине не наблюдалось.
Для повышения эксплуатационной надежности улучшена конструкция пера лопатки и применена более прочная мартенситная сталь ЭИ961-Ш для турбин 800 МВт. При этом вновь возникли проблемы с качеством припайки стеллитовых пластин и попаданием некондиционных лопаток в эксплуатацию. Процесс накопления повреждений происходит более интенсивно при перегрузках турбоагрегата.
Поэтому не случайно повышенное внимание к всемерному снижению перегрузок, возникающих при разгонных испытаниях автомата безопасности и паровоздушных расхолаживаниях цилиндров. Воздействие, которое оказала сконструированная система расхолаживания при развитии трещины ротора высокого давления турбоагрегата Т-110 Южно-Сахалинской ТЭЦ-1 (рисунок В.10), может проявиться и при формировании трещин в замковых соединениях рабочих лопаток и дисковых пазах. Достаточное количество серьезных повреждений лопаточного аппарата в 1995 - 1997 гг. Произошло в момент проверки автомата безопасности (см.
Рисунок В.1). Рисунок В.10. Повреждение ротора ВД турбины Т-110/120-130-5 (ст.
N 3) Южно-Сахалинской ТЭЦ-1 В практике эксплуатации наблюдаются случаи, когда турбинная ступень работает при отсутствии одной и более рабочих лопаток. В целом это недопустимо, особенно длительное время, так как перегрузки рабочих лопаток, находящихся в непосредственной близости к отсутствующей полностью или частично лопатке (лопаткам), создают условия для ускоренного накопления повреждений соседних с поврежденной рабочих лопаток. Такие случаи должны исключаться.
Нерасчетные динамические нагрузки передаются на рабочие лопатки и приводят к накоплению повреждений по длине пера, в хвостовике и на ободе дисков, в том числе и как результат разнотипных нарушений нормального вибрационного состояния. Статистика нарушений нормального вибрационного состояния турбоагрегатов включает случаи накопления повреждений от прогиба роторов, различных задеваний в проточной части, пусков из капитальных ремонтов с весомым остаточным дисбалансом и возможными осложнениями при проведении виброналадочных работ от кратковременных, но высоких уровней вибрации опор. Такое накопление повреждаемости в большей степени скрыто при выявлении причин технологических нарушений, однако оно неизбежно вносит свой вклад в общую картину. Таким образом, вопрос о нарушениях нормального вибрационного состояния неизбежно присутствует при выявлении причин повреждений рабочих лопаток. В общем объеме повреждений лопаточного аппарата весома доля повреждений, причинами которых являются ошибки оперативного персонала при эксплуатации оборудования. Исключение этих ошибок, повышение уровня и качества эксплуатации - важный фактор снижения повреждаемости. Неудовлетворительные динамические характеристики валопровода, вызывающие затруднения и в ряде случаев неизбежно высокий уровень вибрации при виброналадке, также способствуют накоплению повреждений в дисках и лопатках.
Принимая во внимание вышеизложенное, для дальнейшего снижения повреждаемости лопаточного аппарата требуется выполнить следующие мероприятия: - повысить технический уровень эксплуатации турбинного оборудования и исключить ошибки оперативного персонала; - запретить эксплуатацию в режимах, приводящих к повышенному накоплению повреждений лопаточного аппарата, особенно турбоагрегатов со ступенями, выработавшими свой парковый ресурс. Дата Причина останова Наработка на момент останова, тыс. Ч Количество пусков Нарушения за период эксплуатации Повреждения в межремонтный период или по годам Цельнокованые роторы Насадные диски Лопатки Связи Причина повреждения Выполненные работы Организация, проводившая ремонт Результаты Результаты Результаты Результаты осмотра контроля осмотра контроля осмотра контроля осмотра контроля.
Краткая характеристика поврежденной детали Основные размеры Взаимное расположение на роторе мест повреждений (схема) Вид излома (описание, фото или эскиз) Формуляр 2 Эрозионный износ лопаток Тип турбины Станционный N Ступень N Изготовитель Наработка, тыс. Ч Дата ввода в эксплуатацию Количество пусков Частота вращения, об/мин Длина лопаток, мм Скрепляющие связи Описание эрозионного износа (фото или эскиз) Наименьшая площадь поперечного сечения лопатки в зоне эрозионного износа Формуляр 3 Коррозионный износ лопаток и дисков Тип турбины Изготовитель Станционный N Ступень N Наработка, тыс.
Ч Количество пусков Частота вращения, об/мин Описание коррозионного износа (место расположения, плотность, размер и глубина питтингов; фото или эскиз). Формуляр 4 Анализ химического состава и механических свойств металла поврежденных деталей Тип турбины Станционный N Ступень N Наработка, тыс. Данные о вибрации дать вертикальным столбцом, указав по порядку среднеквадратическую виброскорость, размах виброперемещения (1-я гармоника) и фазу (1-я гармоника) F. Приложение Е (справочное) НОРМАТИВНЫЕ ДАННЫЕ О ХИМИЧЕСКОМ СОСТАВЕ И МЕХАНИЧЕСКИХ СВОЙСТВАХ МАТЕРИАЛОВ ЛОПАТОЧНОГО АППАРАТА, ДИСКОВ И РОТОРОВ Для лопаток турбин применяются коррозионно-стойкие (нержавеющие) жаропрочные стали, способные работать в нагруженном состоянии при высоких температурах (до 550 °C) в течение определенного времени и обладающие при этом хорошей жаростойкостью.
В зависимости от структуры применяют мартенситно-ферритные и мартенситные стали. В первых, кроме мартенсита, может содержаться не менее 10% феррита, а вторые имеют структуру из 100% мартенсита после закалки.
Для рабочих лопаток должны применяться в основном следующие марки стали: 12Х13-Ш (КП-45), 20Х13-Ш (КП-50, КП-60), 15Х11МФ-Ш (КП-60, КП-70), 18Х11МНФБ-Ш (КП-60, КП-65, КП-70), 13Х11Н2В2МФ-Ш (КП-70), 20Х12ВНМФ-Ш (КП-60, КП-70). Допускается использование следующих марок стали ограниченного применения: 12Х13 (КП-55), 13Х11Н2В2МФ-Ш (КП-75), 15Х12ВНМФ-Ш (КП-60, КП-70). В качестве материала лопаток, работающих во влажном паре, по согласованию с предприятиями-изготовителями турбин допускается использовать титановые сплавы ВТ 6, ТС5, ВТ20, ВТ3-1.
Требования к химическому составу и механическим свойствам лопаточных сталей и титановых сплавов приведены в таблицах Е.1 - Е.5. Таблица Е.1 Требования к химическому составу лопаточных сталей (ГОСТ 5632).